Introduction
Oil & gas production has increased significantly over the last decade. New technology innovation in drilling and completions like horizontal drilling and fracing have allowed oil & gas operators to achieve record production from wells. The increased production per well located onshore has increased the risk of a spill at these well sites with record production. As a result, this has created the demand for oil spill solutions at the well head to ensure companies meet Environmental, social, and governance (ESG) criteria.
As spilled oil on land prevents water absorption by the soil, spills on agricultural locations or grasslands have the effect of choking off plant life. If a spill occurs in these environments, the highest response priorities are to prevent oil from leaching into groundwater or entering waterways as run-off, and to return the soil to productive use as quickly as possible. The following document provides an overview of the oil production growth in the US, drilling technology and the requirements for spill prevention solutions.
Oil Production in the US
The United States became the world’s top crude oil producer in 2018 and maintained the lead position in 2019 and 2020. U.S. oil production reached 12.0 million barrels per day (b/d) in December 2018 and 12.8 million b/d. Annual crude oil production generally decreased between 1970 and 2008. In 2009, the trend reversed and production began to rise, and in 2019, U.S. crude oil production reached a record high of 12.25 million barrels per day. More cost-effective drilling and production technologies helped to drive the production increases, especially in Texas and North Dakota. U.S. crude oil production declined to about 11.31 million barrels per day in 2020.
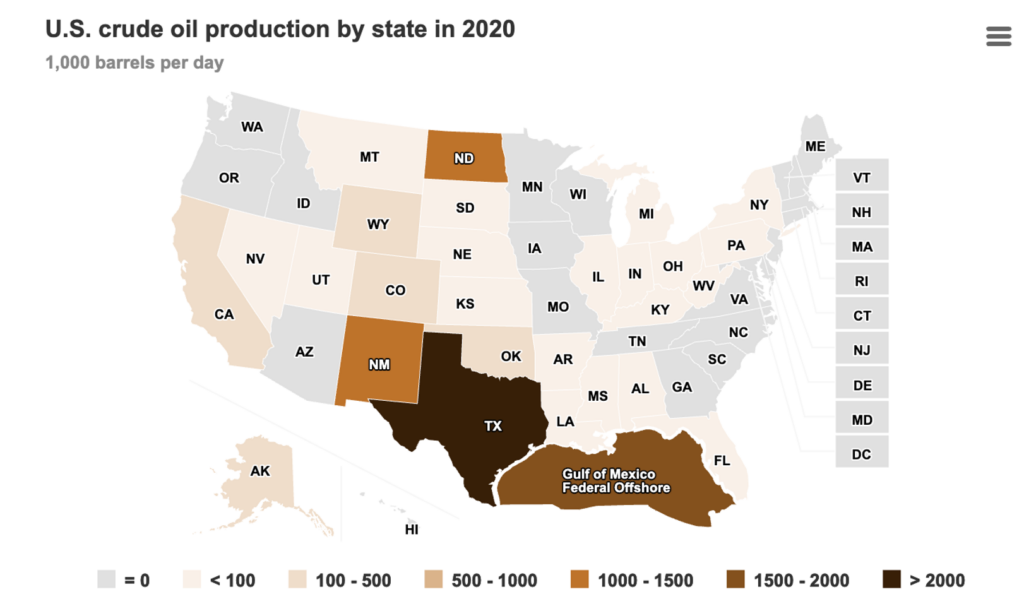
Oil Production in the Permian
Production increases from the Permian Basin (particularly the Midland Basin) contributed to record U.S. crude oil and natural gas production in 2019. The Midland Basin is in the eastern Permian Basin and is within Texas’s borders. During the last decade, hydrocarbon exploration and production in the Midland Basin were driven by development of the organic-rich, lower permeability units within the Wolfcamp and Spraberry formations.
Reservoirs of the basin have been a target for vertical drilling since the 1940s, and vertical drilling generated most of the basin’s production until the mid-2010s. As a result of technological advances in horizontal drilling and hydraulic fracturing, shale intervals of the Spraberry and Wolfcamp formations became the main targets for exploration and production. Production from vintage vertical wells, many of which access the Spraberry and Wolfcamp formations, accounted for about 6% of total hydrocarbons produced from the Midland Basin in 2020. The Midland Basin generated 1.68 million barrels per day (b/d) of crude oil and 5.4 billion cubic feet per day (Bcf/d) of dry natural gas in 2020, accounting for about 15% of total crude oil production and about 6% of total dry natural gas production in the United States, according to Enverus Inc.
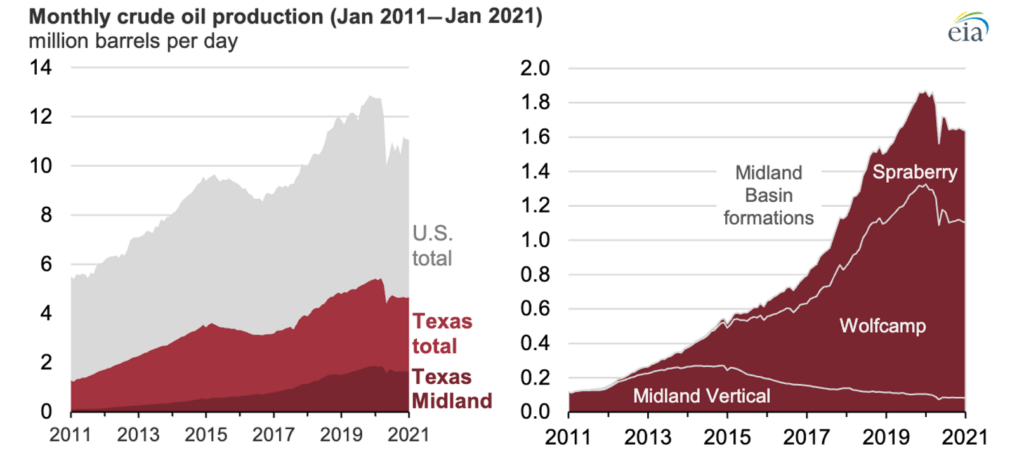
Technological innovation
Technological innovation in drilling and production has caused rapid growth in U.S. oil and natural gas production during the past few years. U.S. tight oil production increased, accounting for 54% of total U.S. crude oil production. Since 2007, the average first full month of oil production from new wells in regions tracked by EIA’s Drilling Productivity Report (DPR) has generally increased.
More effective drilling techniques, including the increasing prevalence of hydraulic fracturing and horizontal drilling, have helped to increase these initial production rates resulting in the need for oil spill solutions. In particular, the injection of more proppant during the hydraulic fracturing process and the ability to drill longer horizontal components (also known as laterals) have improved well productivity.
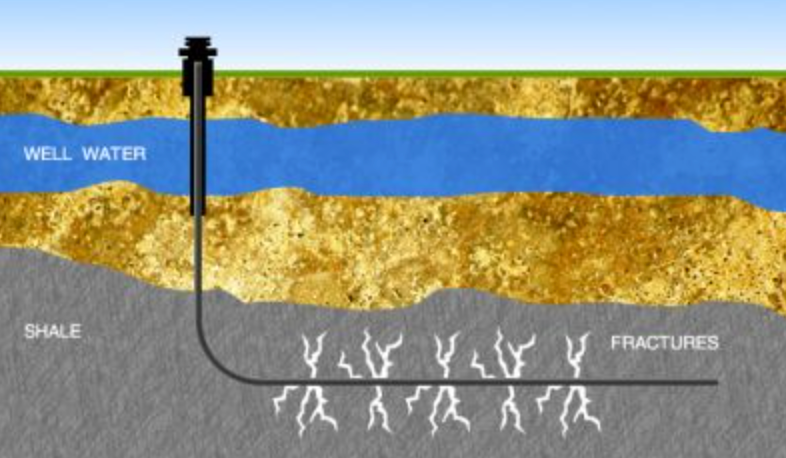
Operators Using Technology to Increase Production
EOG – South Texas Eagle Ford crude oil operations surpassed expectations due to ongoing refinements in completion techniques. During the quarter, 27 wells were put to sales with initial production rates in excess of 2,500 barrels of crude oil per day (Bopd), including nine which exceeded peak production rates of 3,500 Bopd. EOG’s southeastern New Mexico and West Texas operations in the Permian Basin also contributed to ongoing production growth. In addition, modifications in completion techniques and production enhancements combined to make EOG’s rate-of-return results from the Bakken the highest in company history.
Pioneer – The completion optimization program combines longer laterals with optimized stage length, clusters per stage, fluid volumes and proppant concentrations. The objective of the program is to improve well productivity by allowing more rock to be contacted closer to the wellbore.
The current fracture stimulation design, which reflects the 97 wells in the northern Spraberry/Wolfcamp that have been successfully optimized to date, consists of larger proppant concentrations of 1,400 pounds per foot, larger fluid concentrations of 36 barrels per foot, tighter cluster spacing of 30 feet and shorter stage spacing of 150 feet.
Pioneer plans to test further enhanced completion designs this will include larger proppant concentrations up to 1,700 pounds per foot, larger fluid concentrations up to 50 barrels per foot, tighter cluster spacing of 15 feet and shorter stage spacing of 100 feet.
Need for Oil Spill Solutions
Oil & Gas Operators set-up Environmental, Social and Governance (ESG) Steering Committees to monitor performance in the context of an evolving regulatory, legal and stakeholder landscape. The steering committee advises our senior leaders on issues for consideration in enterprise risk management, stakeholder engagement and regulatory and legal compliance. Part of the ESG programs is to ensure that they have adequate oil spill solutions in place. The following are examples of these oil spill solutions for major Operators.
Oxy
Oxy is focused in the Permian Basin of West Texas and southeast New Mexico, one of the largest and most active oil basins in the United States, accounting for approximately 30 percent of the total U.S. oil production.They have a target to control reportable spills of crude oil and condensate to less than 0.0080 percent of production in barrels of oil equivalent on a three-year annual average basis, excluding spills caused by unrelated third parties or natural disasters and net of recoveries.
In 2013, Occidental met its target for controlling the net volume of reportable crude oil and condensate spills, with an annual average of 0.00075 percent of production. This equates to a net volume of 7.5 barrels spilled per million barrels produced, which was better than Occidental’s 2013 target.
ConocoPhillips
ConocoPhillips is a multinational corporation engaged in hydrocarbon exploration. It is based in the Energy Corridor district of Houston, Texas. The company has operations in 17 countries and has production in the United States, Norway, Canada, Australia, Timor-Leste, Indonesia, Malaysia, Libya, China, and Qatar.
They evaluate spill risks and take numerous precautions to prevent spills across our operations. Specialized designs, operating procedures, routine maintenance of our facilities, verifications and process safety best practices play a key role in protecting the environment where we operate. If a spill does occur, established practices, oil spill solutions, and resources are employed to control and mitigate risk.
We are also focused on strengthening our critical incident risk management capability through our systematic, multi-tiered approach to emergency preparedness and crisis management. Hydrocarbon spills impacting a sensitive area and spills greater than 100 barrels are immediately reported to our corporate office. In 2020, we experienced one spill greater than 100 barrels. The spill occurred on land in the U.S. Lower 48 and resulted in approximately 136 barrels being released with an 82% recovery rate. None of our spills in 2020 impacted a shoreline.
Devon
Devon’s current focus is in the oil-rich Wolfcamp, Bone Spring, Leonard and Delaware formations. Drilling activity is yielding outstanding well productivity, driving high-margin growth for the company. With a significant inventory of oil and liquids-rich drilling opportunities that have multi-zone development potential, Devon has a robust platform for future growth.
Devon demonstrates environmental stewardship as we work to minimize our operational footprint. We have a comprehensive oil spill solutions approach to preventing, responding to and remediating spills.
As a responsible operator, Devon works to prevent spills of oil, produced water and other materials from our equipment and facilities. Our environmental-management program includes a Spill Prevention Countermeasures and Control (SPCC) protocol that details the responsibilities, equipment, procedures and steps to prevent, control and provide adequate countermeasures to an unplanned discharge. The protocol helps ensure our compliance with the U.S. EPA SPCC Rule and other environmental rules and regulations. It also specifies the training required for all personnel involved in designing, building and operating oil-handling or storage equipment, including an annual spill-response training exercise and briefing.
Chevron
Chevron is one of the largest producers of oil and natural gas in the Permian. Our holdings total approximately 2.2 million net acres. Approximately 80 percent have either low or no royalty payments. That gives us a strong competitive advantage. In 2019, production in the Permian increased 44 percent over 2018.
Their emergency management efforts are focused on prevention, preparedness, response, oil spill solutions and recovery. We have processes and tools in place to effectively manage emergency response, business continuity and crisis management efforts.
Chevron uses a tiered approach to emergency management. Operating units develop site-specific emergency response and business continuity plans to prepare for all significant risks. The corporate emergency response team is responsible for providing guidance and expertise in emergency response, crisis management and business continuity. The team develops and maintains emergency notification procedures, trains and supports emergency response teams, conducts drills and maintains relationships with organizations that provide emergency response support. Our regional response teams maintain groups of well-trained personnel to assist with emergency response to incidents worldwide.
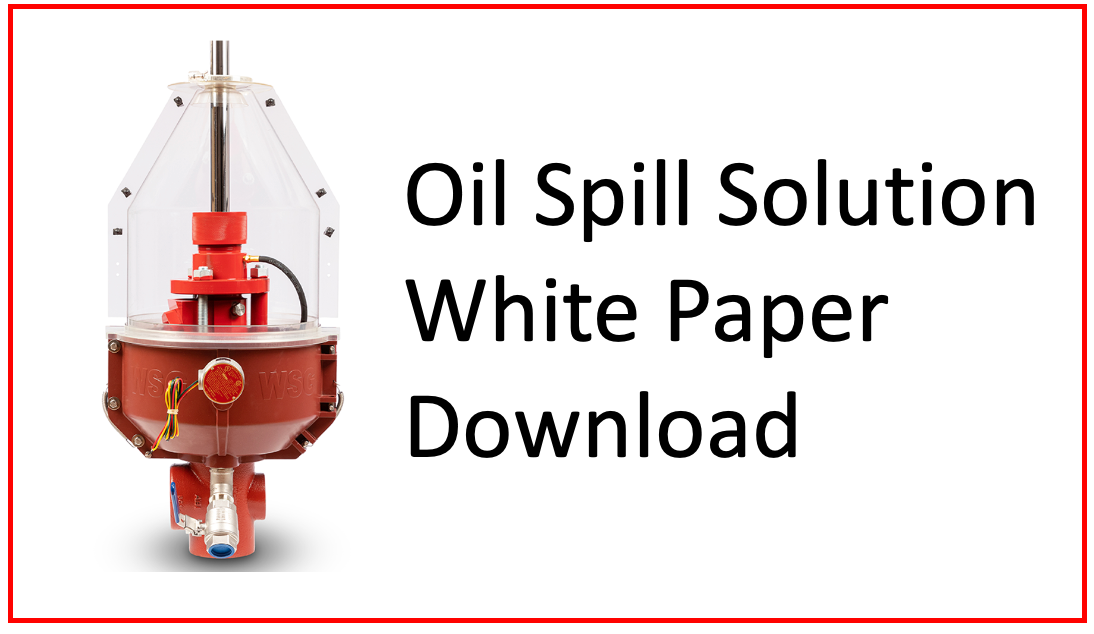
Oil Spill Solutions White Paper
Oil Spill Product Solutions
Oil supplies for our way of life and drives our economy. With the use of this resource comes potential risks. These guiding principles allow the responders to plan for and quickly address an incident, through a well managed process. With zero incident the ever-present goal, should an incident occur, the most rapid and effective response is what is generated though proven principles of oil spill preparedness and response.
- Wellhead Containment – There are a lot of reasons why Oil Companies around the world use secondary wellhead containment on sucker rod pumping units also know as beam pumps. wellhead containment on the stuffing box, producers can reduce the over all environmental footprint of pumping units while reducing the down time caused by spills and leaks. How does stuffing box containment stop the oil? his is done by shutting down the pumping unit once the oil level gets to a certain maximum level. This happens by a float mechanism that acts like that of a float system of a toilet. Once the level reaches the set point, which is set by the pumper, it shuts down the pumping unit stopping the flow of fluid.
- Oil Spill Berms – Spills on land can be contained for recovery by building berms or dikes in the path of the oil flow, using either soil from the area, sand bags, or other construction materials. It is important to make sure the berm does not cause oil to back up and permeate the soil, where it could contaminate groundwater.
- Oil Spill Bioremediation – Certain portions of oil are biodegradable and as such, proper application of certain fertilizers can speed up this process as much as tenfold. Certain plants and their associated microorganisms have also shown promise in speeding up the breakdown of oil. However, even an amplified biodegradation process takes weeks, or even years, and, as such, it is commonly used in conjunction with other cleanup activities.
- Oil Spill Manual Recovery – is the most common method of cleanup and involves teams of workers using rakes, shovels, and other tools to remove oil and debris. The oiled materials are collected in buckets and drums for transfer to a processing station. Workers may also use suction hoses, pumps, and vacuum trucks to recover spilled oil. While manual cleanup is a slow, painstaking process, it generates less waste than other techniques.
- Oil Spill Booms – Oil booms are the most common and popular equipment used in oil clean-up due to their simpler design and easier execution. These are also known as containment booms that enclose the oil to a smaller area and prevents it from spreading further.
- Oil Spill Skimmers – Once the oil is bounded by oil booms, it can be extracted or skimmed easily with the help of skimmers or oil scoops. These skimmers are fitted onto boats to remove the floating oil or greasy contaminants.
- Oil Spill Sorbents – Materials that can adsorb or absorb liquids are termed as sorbents. The use of sorbents is a natural process of oil clean-up. The most common types of sorbents are peat moss, vermiculite (straw), and hay. Some other features of sorbents are listed as follows:
- Oil Spill Burning – It is similar to burning rice husk after yielding rice crop. In this method, the floating oil is set to fire by igniting it safely. It is the most proficient method of oil clean-up, as it can efficiently remove 98% of the total spilled oil.
- Oil Spill Dispersants – When oil cannot be confined to booms, the last option that remains is oil disintegration. Dispersals are chemicals spread over the spilled oil to initiate the disintegration of oil. After disintegration, the surface area of oil molecules increases and it becomes easier for them to form a bond with water. This process takes the bonded molecules deeper in water and makes them available for microbes, which degrade them later on.
US Spill Regulatory Requirements
The EPA’s Spill Prevention, Control and Countermeasure (SPCC) requirements were introduced to protect waterways and the surrounding environment from leaks or spills. These apply to industrial facilities with total above-ground storage tank (AST) capacity of more than 1,320 gallons in containers of 55 gallons or larger, or total underground tank Oil-Rig-Wellhead-Bermcapacity of more than 42,000 gallons.
SPCC regulations include general and specific secondary containment requirements for potential oil leaks, spills and discharges. Examples of general requirements include facility construction features such as impervious berms or retaining walls, gutters, retention ponds or other drainage systems, the supply of sorbent materials to recover liquids, barriers such as skim mats and collection systems such as sumps.
Bulk storage tanks and containers must also meet the specific requirements, which address the potential for major tank or container failures.
The Facility Response Plan (FRP) is the outline how the center would deal with a worst case scenario discharge or threat of a spill.
- Emergency Response Action Plan, which serves as both a planning and action document, which also needs to be maintained as an easily accessible, stand-alone section of the overall plan.
- Facility information, including its name, type, location, owner, operator information.
- Emergency notification, equipment, personnel, and evacuation information.
- Identification and analysis of potential spill hazards and previous spills.
- Discussion of small, medium, and worst-case discharge scenarios and the appropriate response actions.
- Description of discharge detection procedures and equipment.
- Detailed implementation plan for response, containment, and disposal.
- Description and records of self-inspections, drills and exercises, and response training.
- Diagrams of facility site plan, drainage, and evacuation plan.
- Security measures, which may include fences, lighting, alarms, guards, emergency cut-off valves, and locks, etc.
- Response plan cover-sheet.
Conclusion
The United States became the world’s top crude oil producer in 2018 and maintained the lead position in 2019 and 2020. Technological innovation in drilling and production has caused rapid growth in U.S. oil and natural gas production during the past few years. U.S. tight oil production increased, accounting for 54% of total U.S. crude oil production. Oil & Gas Operators set-up Environmental, Social and Governance (ESG) Steering Committees to monitor performance in the context of an evolving regulatory, legal and stakeholder landscape.
Oil spills at well head of the tight oil wells that have record production has resulted in operators to have oil spill prevention strategies. The goal of the programs are to ensure oil does not leach into groundwater or enter waterways as run-off, and to return the soil to productive use as quickly as possible.