ConocoPhillips’ Lower 48 business unit is leveraging technology to improve operational efficiency and reduce cost of supply.
These technologies, including slim-hole drilling, automated drilling, completions, twin fracs, alternative-fuel fracs, refracs and multivariate analysis, are expanding the value of the Lower 48 business covering the Gulf Coast and Rockies and Permian regions.
“These are the technologies I’m most excited about. How can we get more for less? While these aren’t neccessarily new technologies, what’s new is how we’re rapidly transferring technologies and adopting best practices. Because of our scale, the value of these advancements is greatly amplified.” Said Lower Executive Vice President Tim Leach
Slim-hole drilling
Slim-hole drilling has improved rates of penetration by about 30 percent and reduced drilling costs by more than $0.5 million per well.
In this design change, drillers use less-expensive drill bits and smaller-diameter holes, resulting in faster drilling and smaller surface and intermediate casing, all while preserving the 5.5-inch production casing.
“This is not a new concept in the Permain, but it’s a great example of how our combined company is quickly adjusting. Right after the Concho transaction closed, we quickly modified our permits on the heritage ConocoPhillips wells to include a slim-hole design based on our experience. On the very first well, we reduced spud-to-spud days by 50 percent and saved more than $1 million versus AFE (authorization for expenditure).” Leach said.
Automated drilling
The Eagle Ford team, an industry leader in drilling automation, has been using data from past drilling programs to automate drilling and improve curve drilling times by 20 percent.
Stuck wireline events have been reduced by 65 percent.
The team recently drilled its first 14-degree curve, a 40 percent higher build angle than their typical horizontal well. That added an additional 300 feet of lateral or a four percent improvement at no cost.
Twin-frac
Lower 48 has been quick to implement twin-frac, also known as simul-frac technology, in all four of its core basins – Eagle Ford, Bakken, Delaware Basin and Midland Basin.
“We’ve acheived a 40 percent reduction in our frac cycle times, which means we bring production on more quickly. On average, we’re realizing savings of about $200,00 per well, and we’re getting our wells online one to two weeks earlier depending on the lateral length. In 2021, approximately 35 percent of our completions will be done using twin frac, and we expect our use of this technology to increase in 2022.”Leach said.
Alternative-fuel fracs
To reduce fuel cost and emissions in the Permian, the business unit is using electric and dual-fuel fracs.
In 2021, Lower 48 personnel completed 96 percent of the company’s Permian wells using one of these technologies.
During an e-frac, workers use compressed natural gas (CNG) or field gas to power frac pumps. This eliminates diesel use, improves productive time by reducing maintenance, and generates more usable horsepower. It also reduces noise and emissions.
Dual-fuel frac spreads use frac pumps that run off a mix of diesel and CNG.
“As we’ve refined out approach, we’ve been able to routinely reduce diesel usage by more than 65 percent, which not only generates significant capital savings on fuel, but also reduces emissions. Currently, we’re seeing savings of almost $100,000 per well using this technology. And we see additional upside to both dual fuel and e-fracs as we expand out use of lease gas.”Leach said.
Refracs
“By late 2019, we completed 15 mechanically isolated refracs in the Eagle Ford. Now we’ve completed more than 50. We’ve realized a significant uplift in our production rate. On average, our refracs added an additional 75 percent reserve recovery at a fraction of the cost of a new well.”Leach said.
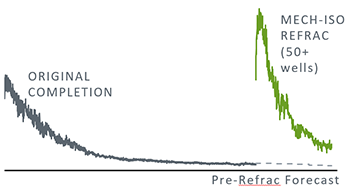
In the Eagle Ford alone, the team has identified more than 350 candidate wells for refracs, and is continuing to test several promising concepts that could improve performance and significantly expand its inventory.
“We’re also beginning to fully leverage our Eagle Ford experience to expand our refrac program into the Permian. We have plans to test refracs in the Midland and Delaware Basin later this year.”Leach said.
Multivariate analysis
Accelerating value from big data, specifically multivariate analysis (MVA), could provide tremendous upside to the Lower 48’s 10-year plan.
“In the Bakken, we’ve used MVA to modify our completion design bsed on individual well chracteristics. We’ve compiled a data set consisting of 43,000 data points from 1,300 wells in the basin, then used MVA to design customization completions for every well based on its specific characteristics. This allows us to avoid things like over-fracking wells, where larger completions are less beneficial, and apply larger completions where is pays off.”Leach said.
Lower 48 expects to realize resource improvements of more than 20 percent and a cost of supply improvement of up to $4 per barrel in the core area using MVA. The business has already begun expanding the MVA application to other assets to create the best development strategy across the entire business.
Technological innovation and driving early adoption of new technologies across ConocoPhillips’ assets is a key component of the company’s strategy to increase efficiency, reduce costs and lower emissions. As an innovation leader, ConocoPhillips maintains a lasting competitive advantage in a rapidly evolving industry.
Energy News
Oil & Gas Permits